

Services
STRATEGIC
Reserve your spots in our strategic workshops, where cross-functional collaboration takes center stage in crafting unified strategic visions for your business goals. These transformative experiences not only encourage the exchange of diverse perspectives but also facilitate the clarification of roles and
responsibilities within your team. Moreover, the workshops are specifically designed to address and tackle weaknesses and threats, providing a comprehensive approach to fortifying your business for sustained success.

Hoshin-Kanri
Breakthrough planning.
A Japanese strategic planning process in which a company develops up to four vision statements that indicate where the
company should be in the next five years. Company goals and work plans
are developed based on the vision statements. Periodic submitted audits are then conducted to monitor progress.

SWOT Analysis
SWOT analysis, a strategic
management method, is employed for
the identification and analysis of
internal strengths and weaknesses,
alongside external opportunities and threats. This meticulous examination is
pivotal in shaping both current and future operations, contributing
significantly to the formulation of
strategic goals.

RACI
RACI Outlines roles and responsibilities within projects or processes using four key designations: Responsible, Accountable, Consulted, and Informed. Through clear role definition, the RACI matrix enhances accountability, communication, and overall project management effectiveness.
DIAGNOSTIC
We specialize in evaluating various aspects of your site, with expertise spanning diverse industries. Our focus includes assessing your organizational culture, the effectiveness of your processes, and collaboration between functions. Gathering insights from team members at every level of your organization is crucial for offering an accurate overview. Importantly, these insights empower you to develop plans to elevate your organization into a world-class entity.

Lean Assessment
A systematic evaluation process used to measure an organization's current state of Lean implementation, identify areas for improvement, and develop strategies for further Lean integration. The primary purpose of a Lean assessment is to gauge the organization's adherence to Lean principles and practices, conducting at regular intervals in order to monitor overall progress during Lean implementation
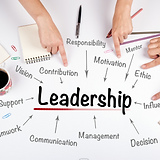
Management System
A systematic evaluation process aimed at collecting and analyzing data to determine an organization's compliance. It involves assessing management, supervisors, and operators across five key areas: Leadership/Change Management, Enterprise Alignment, Continuous Improvement Awareness, Performance Management, and Organizational Interaction. This assessment helps identify the organization's level of adherence to standards, pinpoint areas for improvement, and develop targeted strategies to enhance overall performance and effectiveness.

Company Culture
Evaluates an organization culture across key areas including Quality Policy, Communications, Training, Skills Matrix, and Visual Control. It examines how quality practices are integrated into roles, communication channels, and training processes. Additionally, the assessment scrutinizes the alignment of quality objectives with individual performance feedback and escalation processes for handling quality issues. Celebrating best practices and successes is emphasized to reinforce a culture of continuous improvement and excellence.
TACTICAL
These workshops delve into the tactical aspects of Lean implementation, providing participants with hands-on training and tools to address immediate challenges and opportunities within their organization. Participants engage in practical exercises, simulations, and case studies tailored to their operational context, allowing them to apply Lean principles such as value stream mapping, 5S, Kaizen, Kanban, and error-proofing directly to their work environments. The workshops emphasize team collaboration, and continuous improvement mindsets to drive tangible results and efficiencies. By targeting tactical implementation, these workshops empower participants to make immediate improvements, optimize processes, and lay the groundwork for broader Lean transformation initiatives within their teams and departments.

Analyse &
Foundation
-
Value Stream Map
-
Spaghetti Diagram
-
5s
-
Visual Management
-
Re-slotting the warehouse
-
SWIM Lanes Maps

Implement
& Deploy
-
Flow/Pull
-
Cell Line Layout
-
Standard Work
-
Kanban/Heijunka
-
Set Up Reduction - SMED
-
Poka Yoke
-
VMI

Continuous Improvement
-
A3- Problem Solving
-
Kaizen
-
Gemba Walk
-
Tier Structure
-
LSW
-
Total Productive Maintenance
-
Employee Suggestion Program